Alabama Power employees recommit to safety
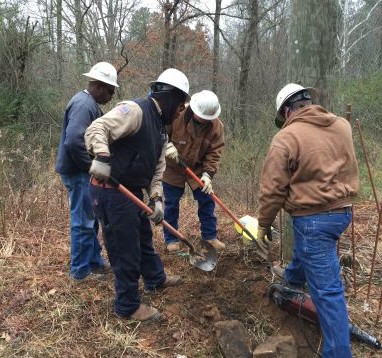
For 2015, Alabama Power has asked all employees to redouble their commitment to working safely, every day and on every job.
Target Zero, the company’s groundbreaking safety initiative, has helped reduce the number of reportable on-the-job incidents by two-thirds since 2003.
But its true purpose is in its name: “Zero.” That means aspiring to zero recordable injuries and preventable vehicle accidents.
It’s a high standard, but not an impossible one, as evidenced by the teams that are meeting the goal.
Target Zero produces a focus on safety
“Target Zero puts your focus on safety every day,” said Osie Cunningham, Crew Foreman of the Selma Line Crew, which has gone 13 years without a recordable incident and 15 years without a preventable accident. “Our workers know exactly what the job details are before they leave every morning.”
“Before, we were more interested in what it takes to get the job done. Safety was a concern, but it wasn’t at the top,” said Johnny Robinson, foreman of Transmission Line Counterpoise (grounding) Crew 43. “After Target Zero came along, I think safety is at the top of everyone’s list now.”
Executive Vice President Steve Spencer said he is proud to see employees making Target Zero work for them.
“The test of Target Zero isn’t just in what it says but in how it’s implemented,” Spencer said. “From Generation to Transmission to Distribution, crews are applying its principles to their day-to-day work. They have turned a goal into an achievement.”
Simple steps to success
One of the first steps for a crew to achieve Target Zero is to perform a job safety briefing (JSB) before starting work.
One recent morning, Robinson’s team met at the General Services Complex (GSC) in Calera before going to work on the Bluff Park District Substation line. The job involved installing copper grounding rods to prevent overloads on the line.
Subforeman Michael “Smoky” Frazier was the day’s point person on safety. Utility Assistant Tyrone Morris checked off a list of hazards to avoid and precautions to take. Crew members all signed the sheet. By the time work began, everyone knew exactly what the job required.
One crew member even repeated from memory the safety credo developed by former company president James M. Barry: “There can be no operating condition which justifies our employees taking the slightest chance in performing their work. We want them always to take the safe way, even though our service may suffer thereby, or our costs be increased.”
Also at the GSC that morning was the Birmingham South Substation Transmission Maintenance Center crew, which has gone seven years without a recordable or a preventable. At 6 a.m., they went over the previous day’s job in south Bessemer. Foreman Anthony Nix led the discussion, which touched on everything from switches that needed adjusting to a potential shortage of “shims” (washer-like lugs for electric bolts).
Target Zero encourages employee engagement
While each crew tailors Target Zero to its circumstances, all crews share several common elements. One is encouraging questions.
“That’s something that’s always been driven into you,” said Wayne Hancock, team leader for the Headland P&C (Protection & Control) Field Services group, which has gone nine years without a recordable or preventable. “You may not want to because you think it’s a silly question. But we encourage you to ask it.”
“The questioning attitude is really big for me,” Robinson agreed.
Another common element is trust. Workers know that they can stop a job at any time if they see something wrong.
“We’re not afraid to stop, any one of us,” said J.P. Smitherman, foreman of Transmission Maintenance Major Equipment Roving Crew 41. “If you see something that doesn’t look right, we commend anyone in the crew to stop.”
On Jan. 20, Smitherman’s team was at Plant Miller to check the source of an oil leak in a transformer. Their JSB covered work procedures, personal protective equipment, precautions, potential hazards, energy source controls and emergency/rescue procedures.
Learning lessons from close calls
Last year, the crew prevented a tragedy by spotting a life-threatening hazard. Outside contractors at Plant Miller were building metal scaffolding far too close to a “hot” 230 kV bus. Crew leader Robert Ford and E&W journeyman Daniel Rasberry saw the problem and ordered the contractors to stand down and remove the scaffolding.
“We knew they weren’t where they were supposed to be,” said journeyman Ryan Easterling. “Daniel and Bob realized it was a very dangerous situation and needed to take evasive action very quickly.”
“The scaffolding was a lot higher than it should have been,” added Rasberry. “One person even felt static electricity. We pulled it down.”
The “close call” – and the lessons gleaned from it – were shared with others so similar situations can be avoided elsewhere. It’s another effective step toward achieving Target Zero.
“We look at what happened and what could have happened and share that with the company as a lesson learned,” said Frazier. “How can it be prevented in the future?”
This mindset is matched by management’s commitment to go the extra mile.
“They never skimp on safety,” said Smitherman. “If it’s something we need, as far as safety training, new tools, they never throw budget constraints in front of us.”
–John Herr