A trip down ‘tobacco road’ set Jason Burns on a path to becoming an Alabama Maker
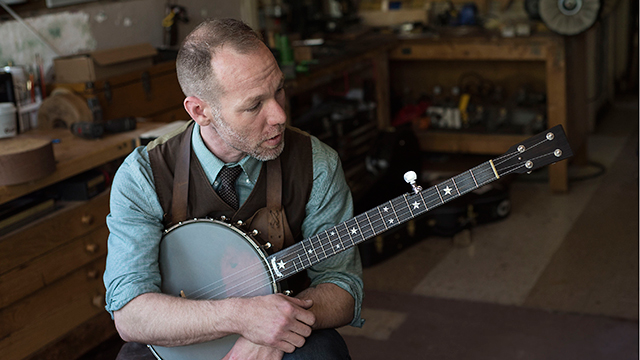
Banjo maker Jason R. Burns in Homewood, Al. (Bernard Troncale/Alabama NewsCenter).
The Maker: Jason Burns, J.R. Burns Stringed Instrument Repair Co.
Jason Burns was the middle school kid just nerdy enough to watch PBS. He had begun playing guitar when he was 12, but hated his axe’s garish red finish. The furniture guys on public television offered the perfect solution: a wood stain made from tobacco.
The Hayden teen sanded the finish off his guitar, and set about creating what he hoped would be a beautiful, rich tobacco stain for it.
“They were using real tobacco, so I found somebody to go down to the store, because I wasn’t old enough to buy tobacco, to buy me a big block of chewing tobacco,” Burns remembers. “I took my mom’s nice pans out and started boiling this tobacco up, and was going to make a stain for that guitar, and it was one of the biggest, stickiest messes. The pots … had burned tobacco in them; it was just gross, it was totally wrong.
“But yeah, that’s how I started out. It was really bad decisions at 13, 14 years old,” he says with a laugh.
Jason Burns crafts custom banjos as a genuine Alabama Maker from Alabama NewsCenter on Vimeo.
From that dubious trip down “tobacco road,” Burns traveled a path that led to him becoming one of Alabama’s most sought after banjo builders. That didn’t happen, though, until he played in a series of punk rock, country and singer-songwriter bands.
What Burns discovered was that his favorite part of touring wasn’t performing. “I wanted to work on guitars,” he says.
In the late 1990s, Burns began doing instrument repair at a sound studio in Tarrant near Birmingham. In 2001, he moved his business to Homewood Musical Instrument Co., the iconic shop owned by Bob Tedrow. Tedrow obviously had a strong influence on Burns, who began dressing like him – pants, shirt and tie with a work apron. More importantly, he shared with Burns a “wealth of knowledge” about instrument repair.
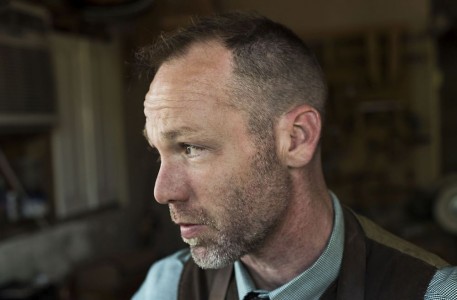
Burns began by building ukuleles and electric guitars before building banjos. (Bernard Troncale/Alabama NewsCenter)
“He would teach me how to repair violins, upright basses, cellos, more extensive work than I was doing,” Burns says. Performing structural work, like repairing broken headstocks, and having access to more tools led to building instruments.
Burns didn’t start out with banjos. Instead, he began building ukuleles and then electric guitars – and a reputation for excellence. About 12 years ago he decided to try his hand at banjos, mainly because he couldn’t afford to buy the one that he wanted for himself. With that decision, he fell into his passion.
“After a while, I started to get a little bit of a name for making banjos so it just kept going,” he says. “For some reason, and I just can’t put my finger on it, it’s one of my favorite instruments to build.”
Burns’ banjos harken back to the late 1800s and early 1900s – “I’m attracted to that era, that time in music” – and are built with a graceful elegance and impeccable attention to detail. He forms rims of maple, walnut and cherry, sometimes clad in brass, and covers them with heads of goat or calf skin.
What Burns builds is “definitely not a bluegrass banjo.” Banjos made for bluegrass have a bright, crisp tone that slices through the din of guitars and fiddles. A Burns banjo has a sound he describes as “a warmer tone, more mellow” and is more of a “parlor instrument.”
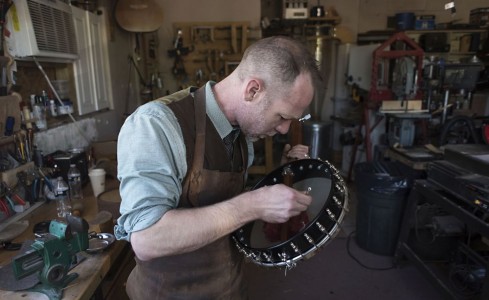
Burns has become one of Alabama’s most sought after banjo builders. (Bernard Troncale/Alabama NewsCenter)
That sound makes many banjo bloggers swoon.
From fretlessinfortwayne on banjohangout.org: “To take a line out of John Henry, ‘it rang like silver and it rang like gold.’ … It’s the finest sounding and constructed open-back banjo that I have ever laid my hands on. And I’ve played a lot.”
And from Brooklynbanjoboy: “I tend to have a sledgehammer approach to claw hammering, and this banjo stood the test. I can also ratchet it down – especially when the wife is trying to read the newspaper in the morning – and Jason’s banjo sounded elegant, articulate and sweet when played with a much lighter touch. … This is a great banjo.”
Burns has built more than 50 banjos, many of them made with special features for customers. Recently, though, he stopped taking custom orders and is concentrating on the banjos he wants to build.
“It’s not the customer’s fault. They have an idea of what would be really cool and really awesome,” Burns says. “But you don’t want to have someone make a bad decision when they’re spending $2,500 to $3,000 for a banjo.”
Nor does he want to spend anywhere from 40 to 120 hours creating something that, to him, feels more like a banjo that Jason Burns built for someone instead of a Jason Burns banjo.
“I want to be able to control it more, to be excited about every time I build,” he says. That’s because with a thriving repair business and a wife and two small children, there’s not as much time as he’d like for building banjos.
“It’s gotten hard to find any time to make banjos,” Burns says. “And I make a lot more money doing repair work than I do banjos.”
Not that he’s complaining. “It’s one of the best times, and one of the hardest, most stressful times,” he says. “There’s just a lot going on. It’s very exciting, very hard, very fatigue-driven. And very fulfilling.”
The Product: Hand-built banjos
J.R. Burns Stringed Instrument Repair Co.
Jrburns333@gmail.com
205-879-1690
Alabama Makers explores the artisans, crafts people, carpenters, cooks, bakers, blacksmiths, designers and others making original and extraordinary items in our state. If you know an Alabama Maker, let us know at alnewscenter@outlook.com.